Wed 17 March 2004 |
First up Dad changed the blade on the band saw. The new one is MUCH better. It is a bi-metal variable pitch blade - and goes through AL like butter. Worth the time and effort to get a suitable blade. | 
|
I continued with the canopy latch handle fabrication. The parts are now ready to be used on the real thing (which is still a little way off). | 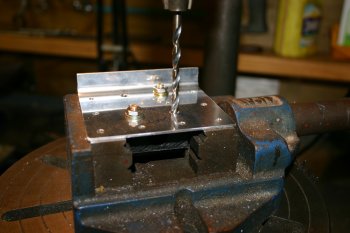
|
Next was then other various fabrication parts. Normal processes, cut, drill, edge, smooth etc. Dad was also continuing with the fabrication of various pieces of shaped AL angle. | 
|
I then went back to the hat section and the mounting of the UWHM plastic block via nutplates. | 
|
The recesse for the cross-bolt is two 1/2" holes joined along the long edge. Rotorbroach for each end and rotor burr for the joining up. Finish with file and scotch brite. | 
|
Then we tried something a little different! After chatting with Dad about the hole for the canopy latch we discuss the idea of using a router for creating the slot in the skin. We dug out a new router bit (4mm) and set to work on the skin. | 
|
The result was REALLY good. We have the process for real fuse, although we need a slightly smaller bit. | 
|
This is the end product of the canopy hinge structure work I've been doing. The hinge points haven't been drilled yet, I'll wait until everything is cleco'd into the straight fuse. | 
|
This is the problem poser for the day. The 24A drawing contradicts it self. The mid fuse support is drawn as flange to the right (as shown) but this means the 90 degree angle isn't at the top and therefore the forward tip of the support is well below the top edge of the firewall. One option is the flanges should point to the left and the right angle will then be at the top and the heights should work, but this is markedly different from plan. An email to VANs was sent - I'll let you know. | 
|